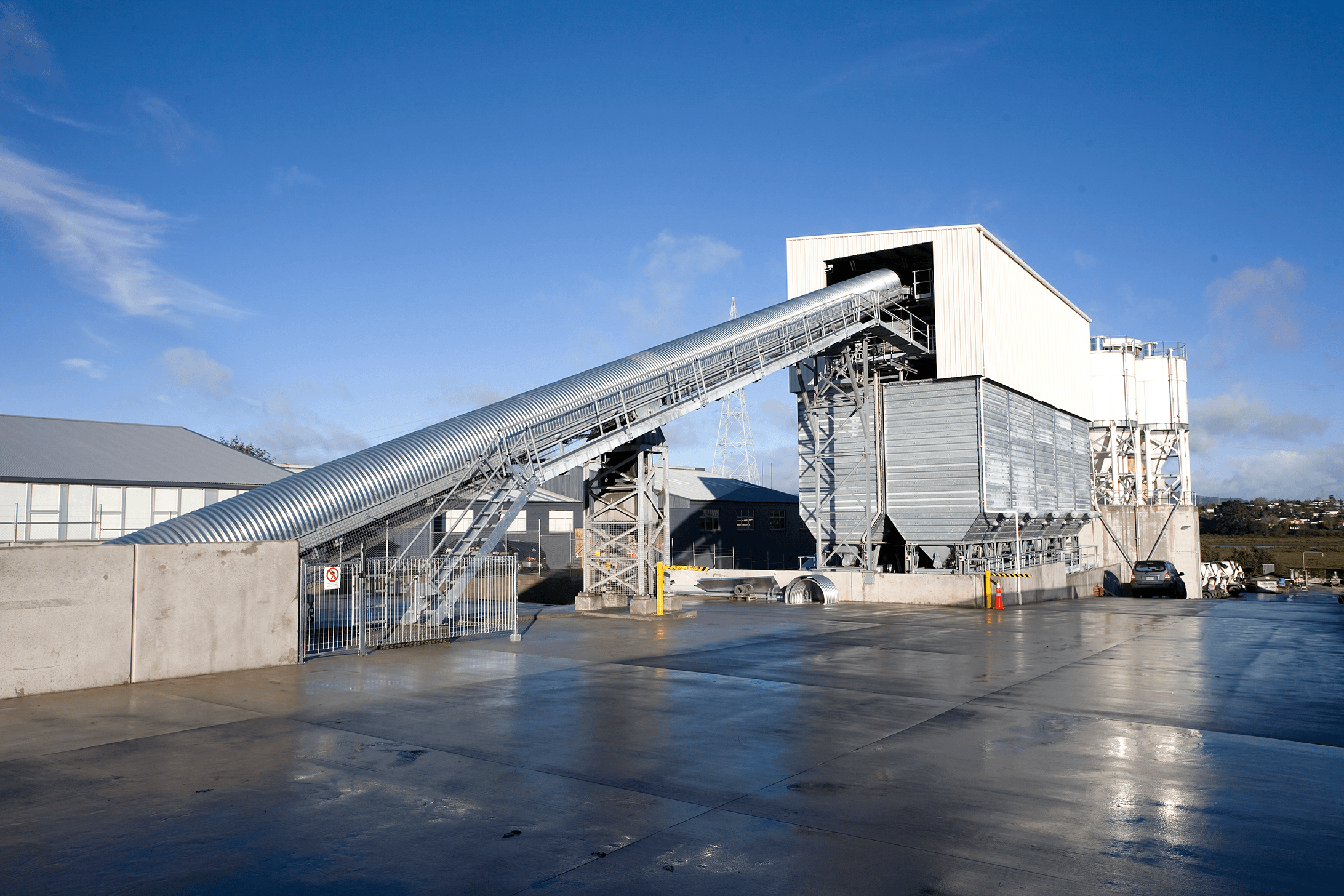
Modular Batching Plant
WETBETON batching and mixing plants are state of the art for concrete production. NEXUS aggregates hoppers are together with the mixer, the central component of the plant; key features of NEXUS hoppers are availability in different sizes and capacities, high modularity, possibility of expansion, high inclination of bin walls and cones (for a proper material flow), prevision for liners, full galvanization, industrial production with highest standard processes.
Aggregates
The aggregate receiving hoppers can be of different types depending on
the space available and the customer’s needs.
Underground
Underground fully overdrive or partially overdrive (25 m³)
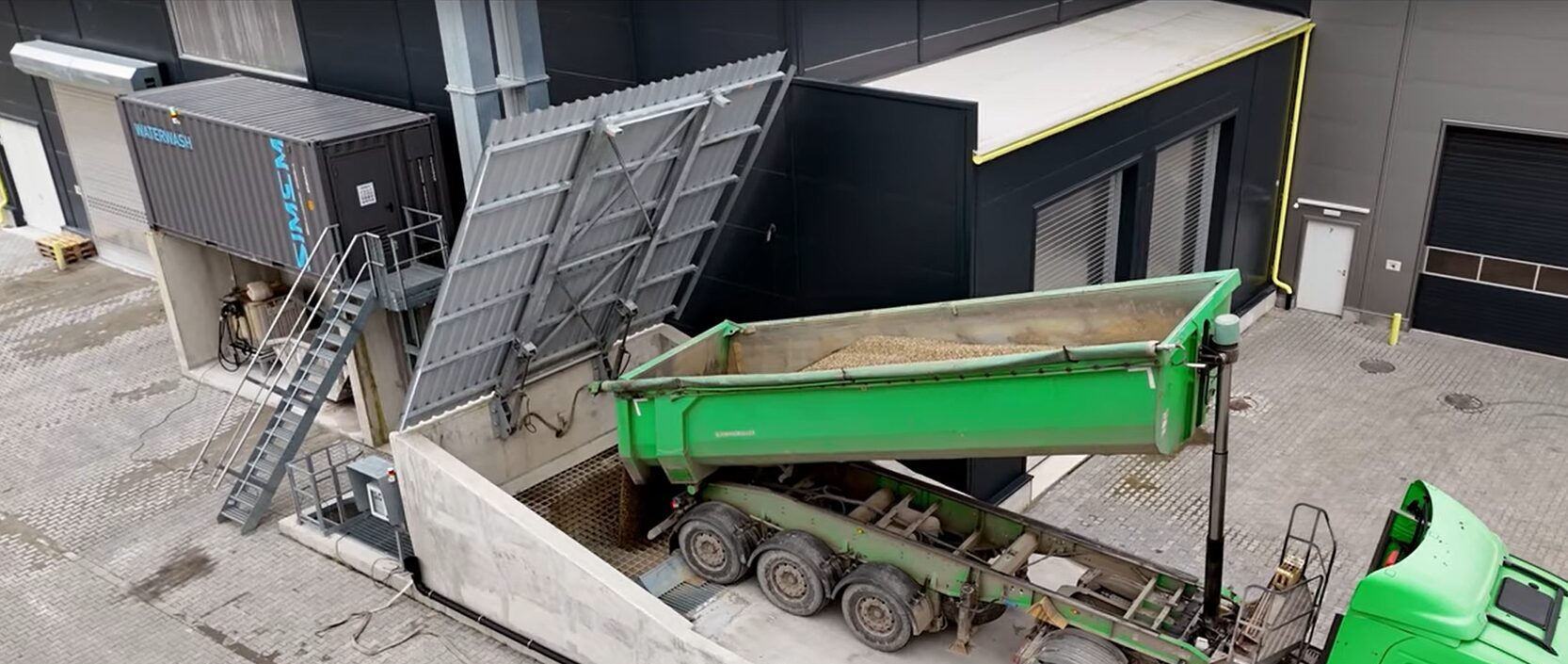
Above ground
Above ground
semi-driveable (25 m³)
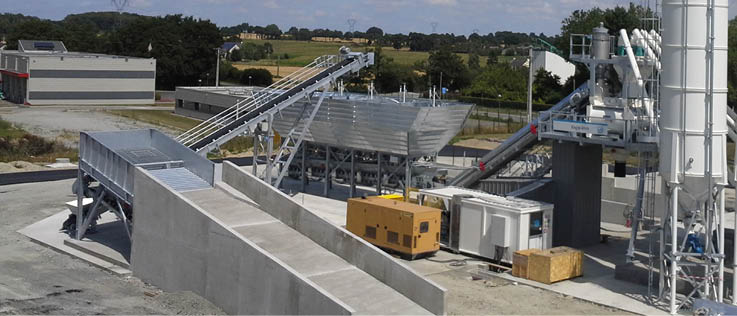
Wheel Loader hoppers
Hoppers for wheel loaders
(up to 10 m)
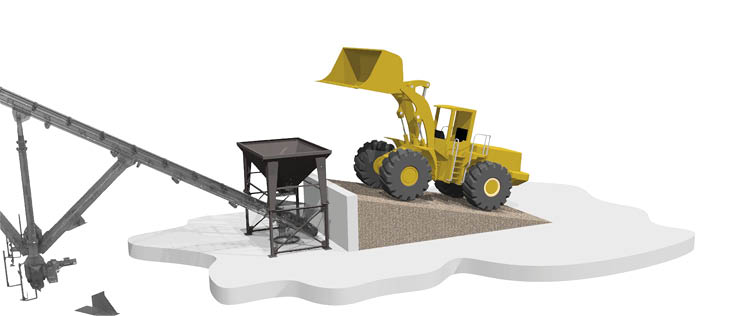
The aggregate conveyor belts can be combined depending on the
available space and the customer’s needs.
Conveyor Belt
Radial movement for automatic distribution of aggregates
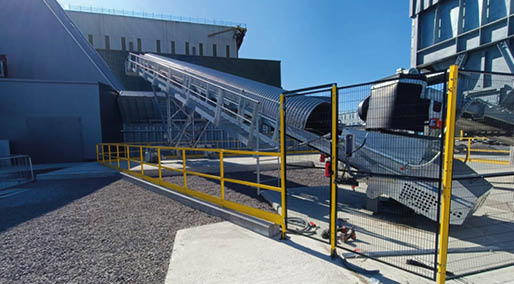
Elevator
Inclined belt together with the distributor above the aggregate bins
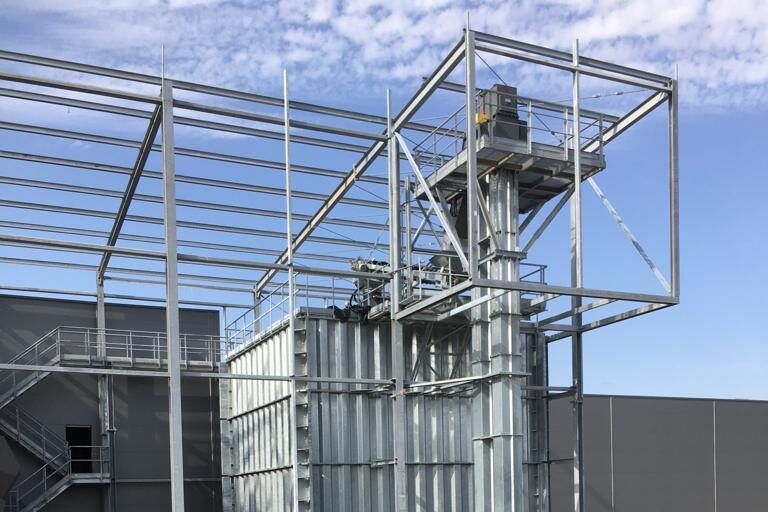
Distributor belt
Bucket elevator together with the distributor belt to optimize small spaces
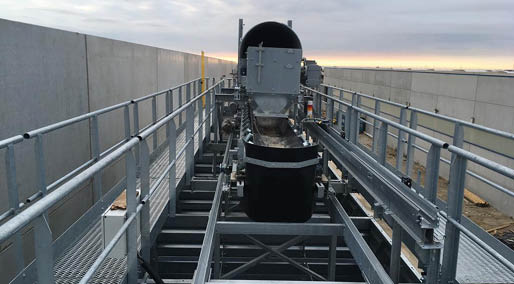
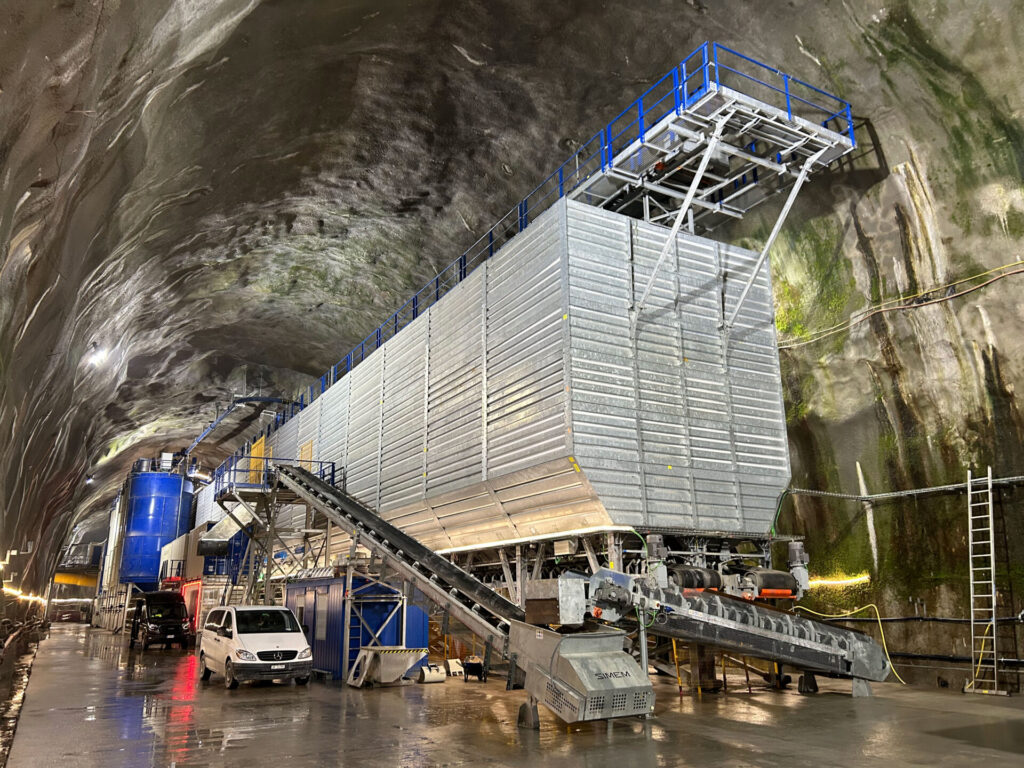
Aggregates storage hoppers
In addition to the main mixing body, the other key component is the NEXUS hoppers: available in different sizes and capacities, they are highly modular. The NEXUS system allows for maximum flexibility in configurations, both in terms of number and capacity for each compartment. Just like Lego, the modules are joined together with bolts, and therefore they can be modified/moved more easily. The structure is entirely galvanized and meets the highest industrial standards in terms of quality and performance.
Silos
We realize solutions for bulk materials handling and storage. We supply a wide range of vertical storage as monolithic or bolted panels solutions with volume and quantity based on the project needs. All silos are fully equipped with sensors, fitlers and fluidifications
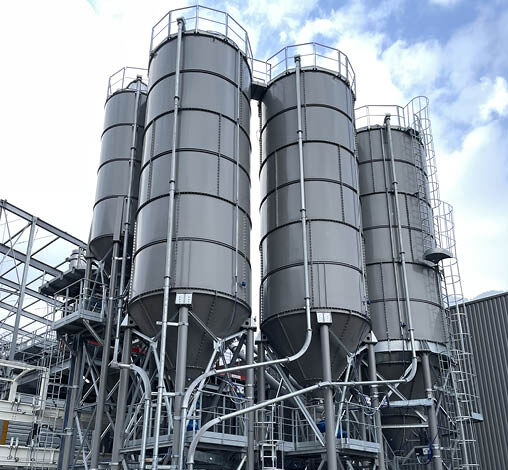
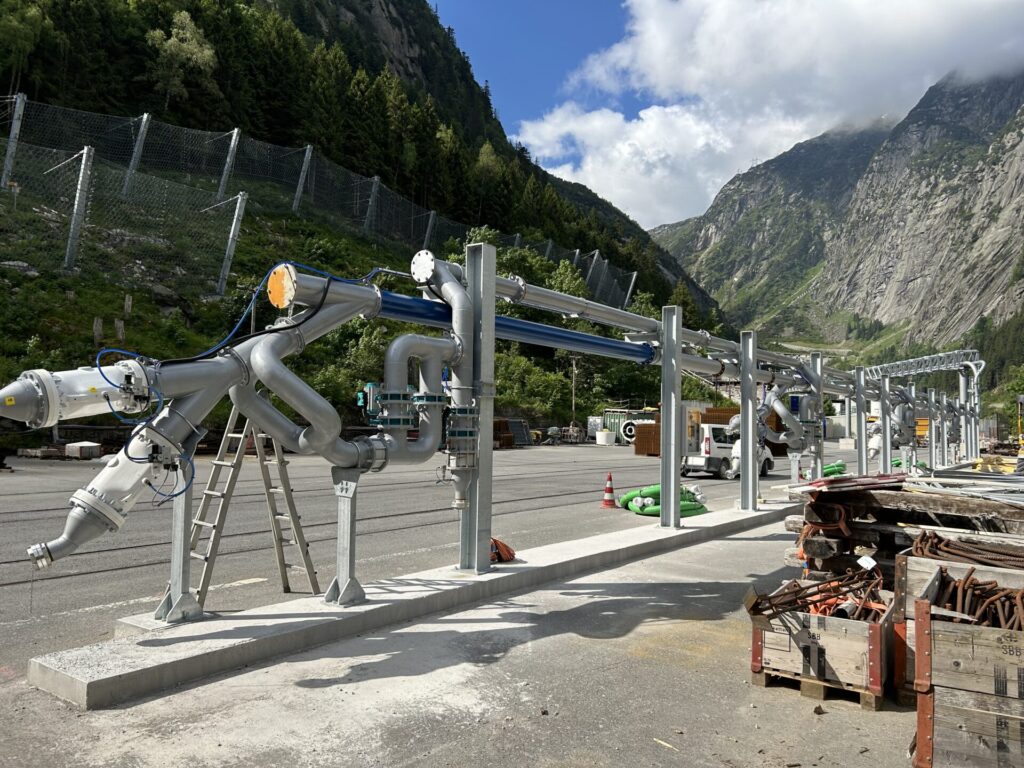
Poweders Transfer
We supply a wide range of screw conveyors depending on the application and on the type of powder to transport. We provide also pneumatic transfer solutions to handle powders from big silos to silos OR from wagon to silos OR from port storage to barge storage…
Aggregates Dosing & Transfer
The weighing of the aggregates is done very accurately by mean of electronic load cells; the process can be cumulative on a single weighing hopper with an extracting belt conveyor, or alternatively through individual scales for each aggregates type. The aggregates transfer system from the weighing hopper to the mixer, can be processed through skip hoist to minimalize the footprint or with inclined belt conveyors.
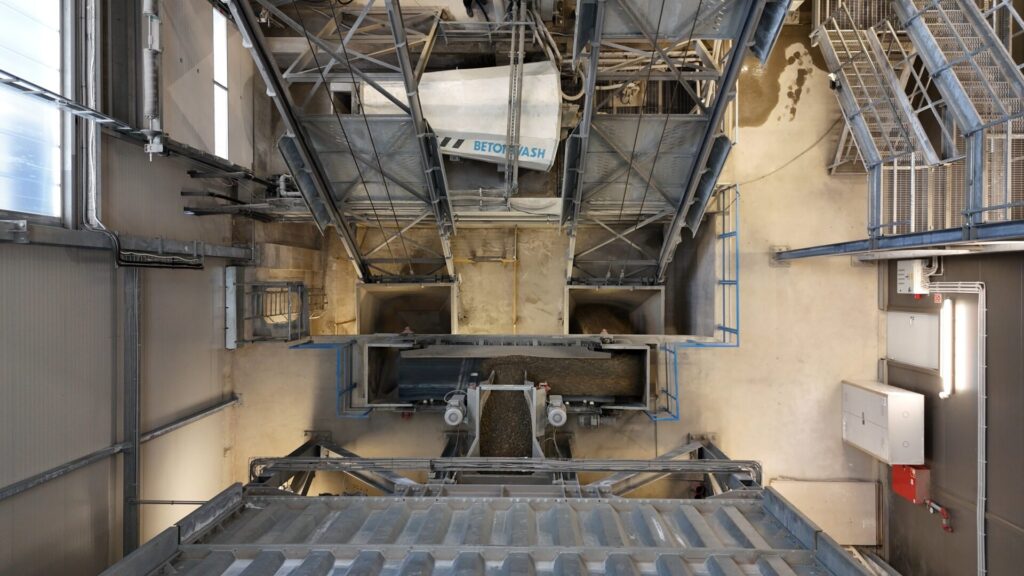
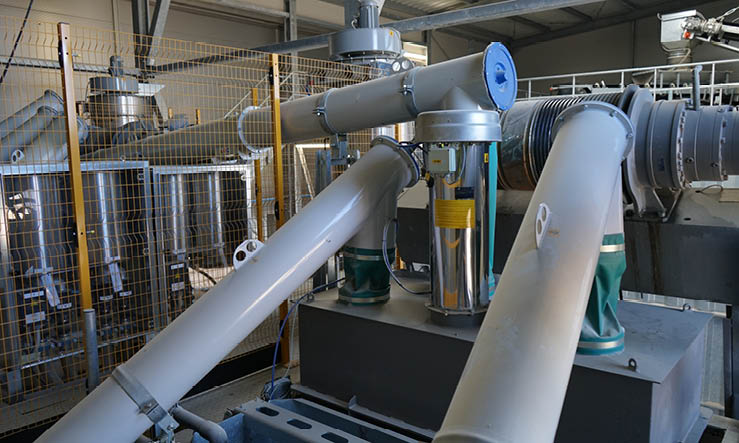
Dosing Process
The cement is transported from silos through screw conveyors while the additives arriv from the appropriate containers. The water is added through appropriate pipes. Everything is dosed according to the recipe and discharged by gravity.
Mixing
WetBeton plants, combined with our planetary or double-axis mixers, allow us to adapt the plant configuration based on the characteristics of each construction site in terms of capacity and typology. The design of Simem XENTRIX planetary mixers has a patented central charging solution for cement, water, and admixtures which makes it a leader in its class with the best possible mixing action. The Simem RHYNO horizontal twin-shaft mixer represents excellence in the field of mixing thanks to a robust design, intuitive paddle adjustment and mixing action with the innovative DYNA-FLOW technology.
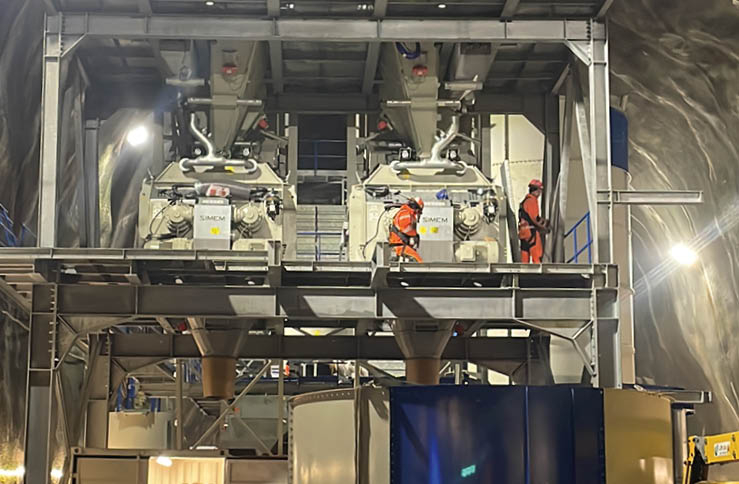
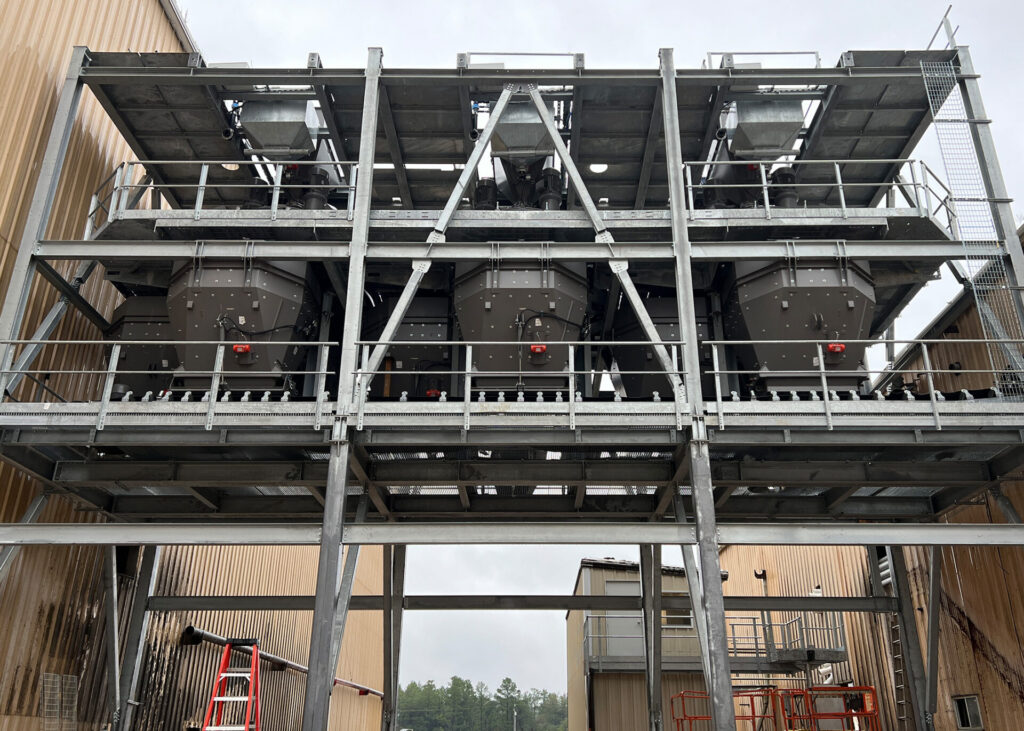
Concrete Discharge
We provide different solutions for the concrete discharge. Especially in precast and RCC production, holding hoppers are one of the main solutions. Standard cones are available for discharge into truck mixer or bucket.
Verschiedene Lösungen für die Betonverladung sind verfügbar.
Nachbehälter (meist in der Fertigteilindustrie verwendet) oder diverse
Auslasstrichter die sich an die Anforderungen des Kunden richten.
Concrete Distribution
For applications in the precast industry, Simem has developed over the years a series of highly reliable machines for the transport and distribution of concrete. The Pelican wagons can be developed on a double line to be loaded by two mixers. They travel at a speed of 180 m/ minute and have a capacity of 1 to 3 m³. They unload the material through a rotating movement and are controlled by a PLC system. A washing station is also available.
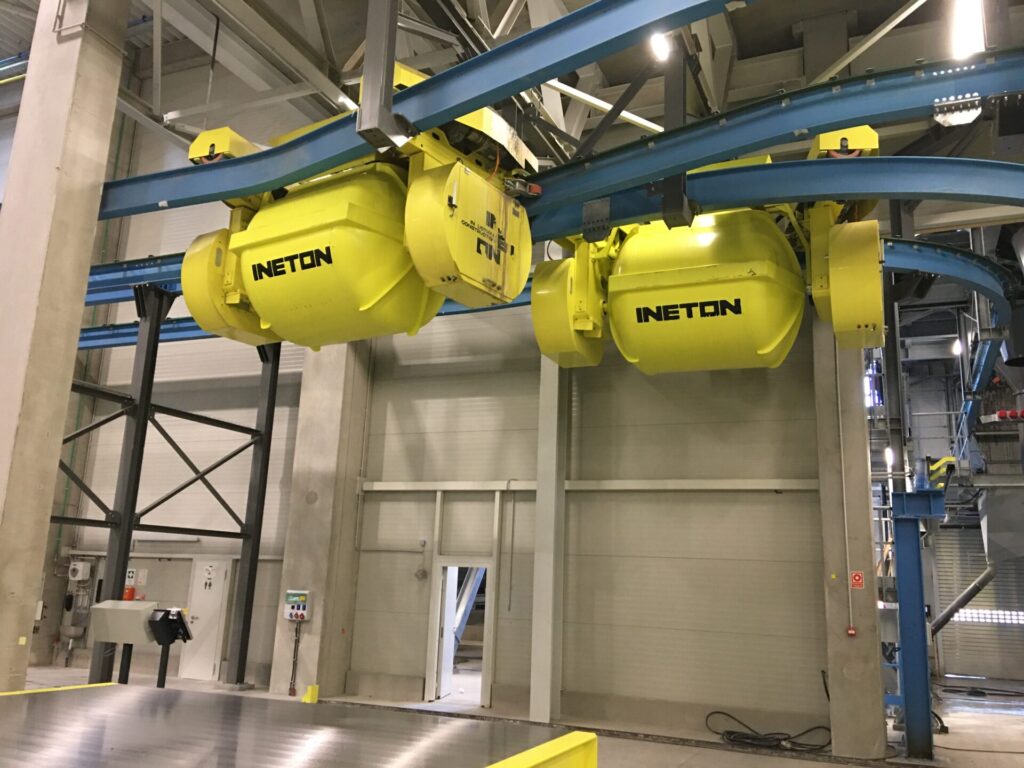

Simem@tic 3.0
SIMEM@TIC is the automation control system with a friendly interface which displays all essential plant operation information. A full process sequence view (loading, weighing, recipe, discharge, washing, production listing, pending orders) with self-adjusting software for a predictable and repeatable outcome. All production data is recorded and stored in SQL database format providing detailed record of concrete production.